Bitumen emulsion unit 2 m3/hour production capacity

The UVB-1- bitumen unit is designed for the production of anionic and cationic bitumen emulsions, which are used in road construction for the following purposes:
– tack-coating of the old road pavement base before laying new asphalt concrete;
– preparation of cold asphalt concrete mixes;
– surface treatment of pavements;
– thin protective coatings;
– road top patching;
– dampproofing of buildings and structures;
– soft roofs construction and repairing.
. The UVB-1 also features injection of various components into the emulsion, such as stabilizers, viscosity adjustment and adhesion materials, as well as latex, which allows to make a product more stable to high and low temperatures. If latex modification is required, the plant features an inlet for latex injection module, located after the hydrodynamic mixer, before the mill, through which the product passes for full mixing with the emulsion.
Different types of emulsion (anionic or cationic) can be modified with anionic and cationic latexes respectively.
Plant UVB-1 (hereinafter init) designed for production of bitumen emulsions (see figure 1 and 2) is a semiautomatic unit, which consists of several sections mounted on a common frame and connected by means of pipelines:
Figure 1 – Unit general view (control panel side) Figure 2 – Unit general view (bitumen pump side)
Item | Description | Item | Description |
1 | Frame | Faucets for | |
2 | Blending tank | 14.1 | Water |
3 | Pumping unit | 14.2 | Blending |
4 | Mill | 14.3 | Flux |
5 | Water pump | Flow indicator (rotameter) of | |
6 | Blending pump | 15.1 | Water |
7 | Flux pump | 15.2 | Blending |
8 | Hydrodynamic mixer | 15.3 | Flux |
9 | Blending mixer | 16 | Pneumatic bitumen three-way valve |
10 | Water phase mixer | 17 | System of heated bitumen pipelines |
12 | Control panel (CUU) | 18 | Pipelines of oil heating |
Gauging tanks section | |||
13.1 | Acid | ||
13.2 | Emulsifier | ||
13.3 | Adhesive additive | ||
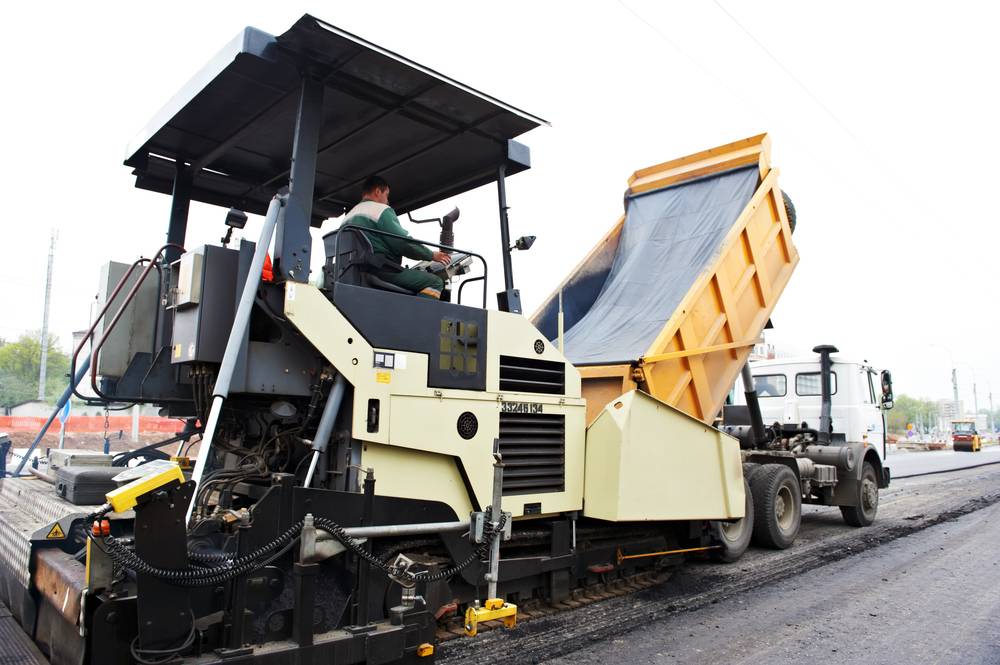
Tracked paver at asphalt pavement works for road repairing
Parameter | Value |
1 Maximum capacity (taking into account preparation time), m3/h | 2* |
2 Minimum bitumen consumption (at penetration rate 90…130), m3/h | 1,5 |
3 Water consumption, m3/h | 0,6…1,5* |
4 Flux consumption (at bitumen penetration rate less than), dm3/h | 0…50* |
5 Acid consumption, dm3/h | 5…20* |
6 Emulsifier consumption, dm3/h | 5…20* |
7 Adhesive additive consumption, dm3/h | 1…20* |
8 Maximum input bitumen pressure, MPa | 0,2 |
9 Pressure of bitumen supplied the blender, MPa | 1,4…1,6 |
10 Water phase pressure supplied to blender, MPa | 0,2 |
11 Input bitumen temperature, оС | 140-160 |
12 Input water temperature, оС | 40-60* |
13 Maximum emulsion output lift, (m) | 15 |
14 Maximum power consumption, kW | 17 |
15 Power circuit voltage at 50Hz, V | 400 |
16 Compressed air pressure, bar | 4…6 |
17 Air consumption, dm3/min | 250 |
18 Maximum dimensions, mm: | |
-length | 2340 |
-width | 2080 |
-height | 2080 |
19 Maximum weight, kg | 1410 |
* Depending on the formula of produced emulsion!