
Asphalt emulsion production benefits.
A number of technologies allow asphalt emulsion to be mixed at much lower temperatures. These involve mixing with petroleum solvents to form “cutbacks” with reduced melting point, or mixtures with water to turn the asphalt/bitumen into an emulsion.
Using asphalt in road construction requires the support of the minimum possible viscosity of the material. Technically, this is achievable by one of the following methods:
- heating to process temperature;
- liquefaction by using thinners;
- emulsification of asphalt in water (making asphalt emulsion).
– The first method has significant drawbacks, especially in terms of energy costs of heating the mineral materials, the limited time of setting up the road top and the harmful impact on the environment.
– The second method involves the use of expensive thinners, which also contaminate the environment and pose a fire hazard.
Using asphalt emulsions is different from the two methods above, since it does not require heating and can be combined with cold and moist mineral materials. In practice, the reduction of energy costs using emulsion technologies can reach 40% compared to the traditional hot process. Bitumen economy is 20 to 40%.
Asphalt emulsion applications:
- formation of road bed;
- formation of road revetment layers;
- construction of rode pavement;
- maintenance and repairs of pavement.
Principle of Operation: Manufacturing of Asphalt Emulsion with GlobeCore UVB-1
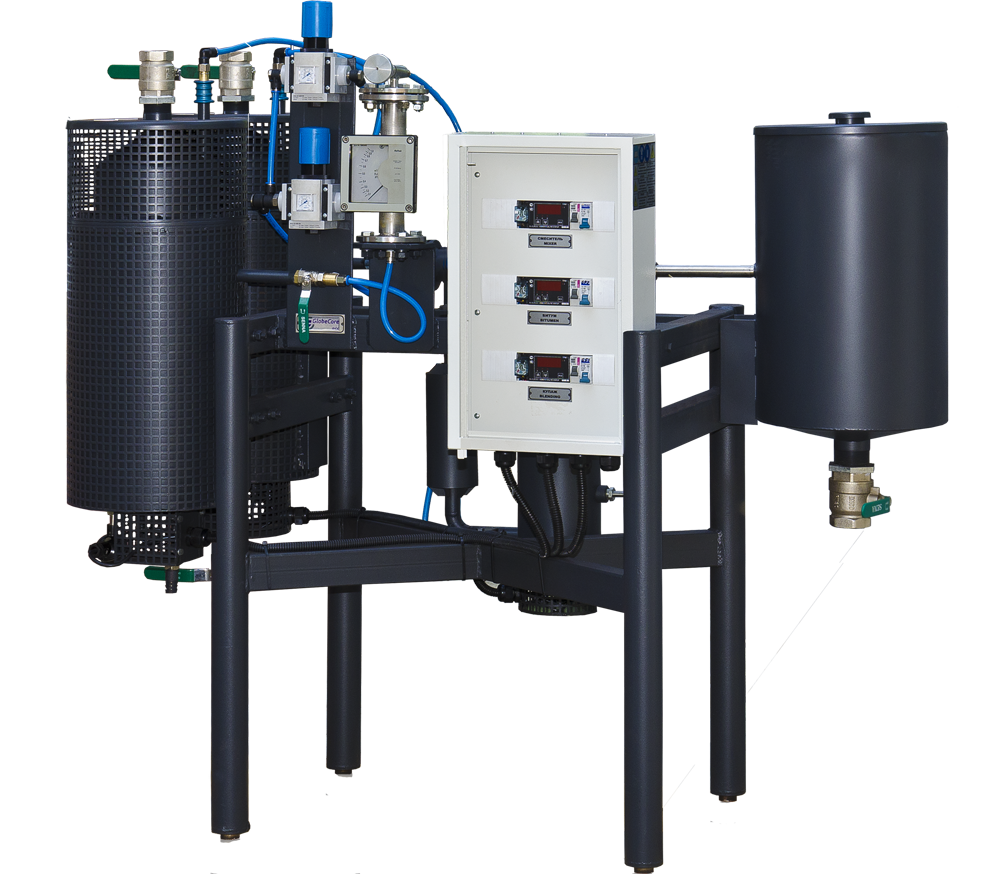
UVB-1
The UVB-1 is designed for production of asphalt emulsions, operates in semi-automatic mode and consists of several autonomous components mounted on a single frame and connected by piping. Emulsion is made by consequtive mixing of components at certain pressure and temperature.
UVB-1 advantages
GlobeCore unit for manufacturing of bitumen emulsion offers the following advantages:
- Production of high quality asphalt emulsion regardless of initial bitumen quality by adding plasticizers, adhesion additives and thinners;
- Production of all emsulion types, CRS, CMS and CSS-1,2, as well as anionic emulsion of corresponding types, including subtype h;
- Blend concentrate is diluted by water directly in the unit;
- Safety of operation (emergency interlocks in place);
- Emulsion complies with ASTM D 2397-98 and D977-98;
- Small footprint;
- Simple servicing and operation.
Client benefits from purchasing this unit for manufacturing of asphalt emulsion: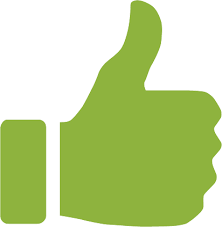
- independence of asphalt emulsion suppliers and construction material market fluctuations;
- repair and construction capability from early spring to late fall;
- bitumen economy;
- power savings;
- client personnel training;
- starting and commissioning of the unit on site (if necessary).